
By concrete shape Flat Wall System įor Flat Wall System ICFs, the concrete has the shape of a flat wall of solid reinforced concrete, similar to the shape of a concrete wall constructed using removable forms. Organizations whose first concern relates to the fabrication of the forms classify them first by the characteristics of the forms themselves. Organizations whose first concern relates to the concrete classify them first by the shape of the concrete inside the form. Insulating concrete forms are commonly categorized in two manners. Regulated humidity levels and mitigated mold growth (hygric buffer).Backing for drywall or other finishes on the interior and stucco, brick, or other siding on the exterior.The form material on either side of the walls can easily accommodate electrical and plumbing installations. Space to run electrical conduit and plumbing.Good surface burning characteristics rating.Like other concrete formwork, the forms are filled with concrete in 1-foot to 4-foot high "lifts" to manage the concrete pressure and reduce the risk of blowouts.Īfter the concrete has cured, the forms are left in place permanently to provide a variety of benefits, depending on materials used: Reinforcing steel bars ( rebar) are usually placed inside the forms before concrete is poured to give the concrete flexural strength, similar to bridges and high-rise buildings made of reinforced concrete. Polyurethane foam (including soy-based foam).Polystyrene foam (most commonly expanded or extruded).Insulating concrete forms are manufactured from any of the following materials: ICF construction is now part of most building codes and accepted in most jurisdictions in the developed world. The adoption of ICF construction has steadily increased since the 1970s, though it was initially hampered by lack of awareness, building codes, and confusion caused by many different manufacturers selling slightly different ICF designs rather than focusing on industry standardization. This patent claimed a parallelepiped-shaped brick having a central cylindrical cavity, connected to the upper and lower faces by countersink.
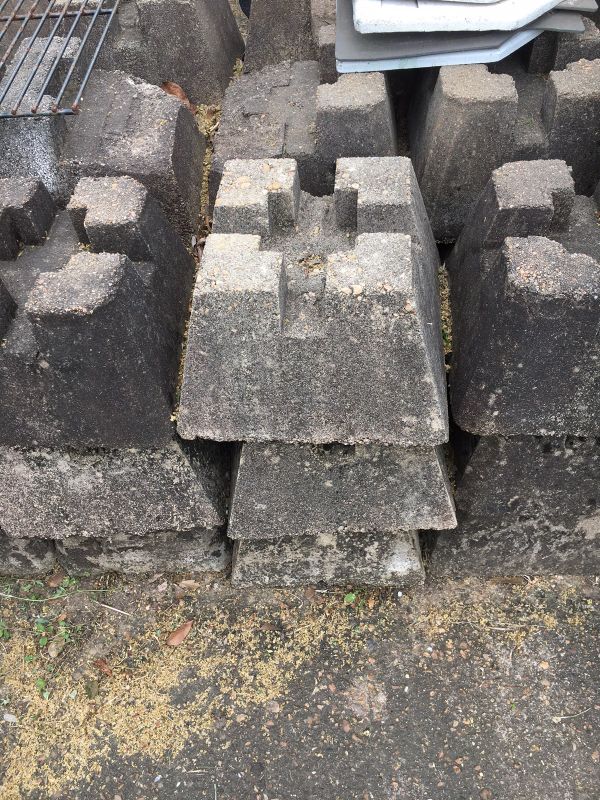
It is right to point out that a primordial form of ICF formwork dates back to 1907, as evidenced by the patent entitled “building-block”, inventor L. Canadian contractor Werner Gregori filed the first patent for a foam concrete form in 1966 with a block "measuring 16 inches high by 48 inches long with a tongue-and-groove interlock, metal ties, and a waffle-grid core."
Concrete deck blocks install#
Install the remaining deck boards using the same techniques, spacing them evenly.The first expanded polystyrene ICF Wall forms were developed in the late 1960s with the expiration of the original patent and the advent of modern foam plastics by BASF. Install the next deck board with two screws in each standard joist, spacing the two deck boards by about 1/8 inch apart. Fasten the deck board to the joists with 2-inch deck screws (for 1-inch-thick lumber) or 2 1/2-inch screws (for 1 1/2-inch-thick lumber). Position the holes slightly off-center so they won't interfere with the frame screws. Alternatively, you can place the first and last boards so they overhang the end joists by 1 inch, or so, for a finished look just be aware that you won't have the same overhang at the sides of the frame.ĭrill pairs of pilot holes aligned with each standard joist, with one hole going into the end joist and one into the standard joist. Place one deck board along one long side of the deck frame so it is flush with the outside face of the end joist. Measure all of the 12-foot-long deck boards, and trim any as needed so they are 144 inches each. Do the same to mark the other end joist.Īdd two more standard joists inside the frame so each end is set between a pair of layout lines, making sure the tops of the joists are flush. Drill pilot holes, and fasten through the end joist and into the standard joist with three 3 1/2-inch screws at each end.

Measure from the inside of one corner of the frame and make a pair of marks every 16 inches along one of the 12-foot end joists. Place the two end joists over the ends of two of the standard joists to create a 120-inch-by-144-inch rectangle.ĭrill pilot holes, and fasten the pieces together with three 3 1/2-inch deck screws at each corner, using a drill. Measure the two 12-foot 2x8s if they're anything over 12 feet, trim them to exactly 144 inches (lumber often runs a fraction of an inch longer than the nominal dimension in this case, 12 feet).
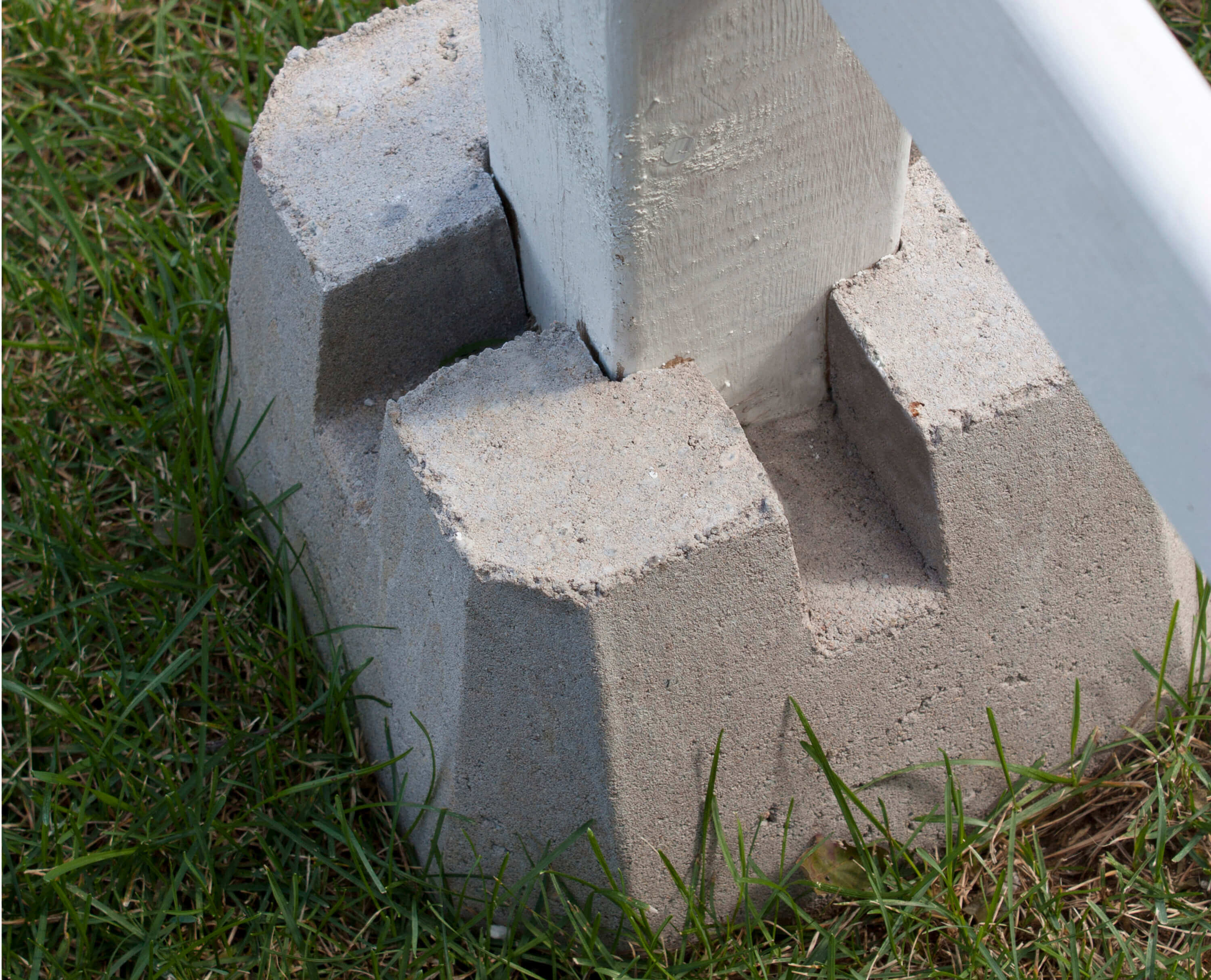
Cut 10 pressure-treated 2x8 boards to length at 117 inches, using a circular saw or power miter saw these are the standard joists. If necessary, you can also build the deck on top of the concrete blocks.
